Co-operation with scientific and academic institutes on the development of laser technologies, processes, and methodologies is very important for their subsequent wider and easier integration into the real-life environment of industry. LASCAM has been co-operating on such projects for a long time. One of the most significant, in which we had the opportunity to participate, was the development and launch of a unique multifunctional laser workplace with four integrated laser technologies – 3D laser cutting, powder coating, welding using WOBBLE technology, and wire additive 3D printing.
Unique integration of four laser technologies into one automated development site
First installation of a multifunctional cell in the European scientific sphere
For the first time in Europe, a comprehensively prepared multifunctional cell has been installed for scientific purposes. It was developed and launched for the needs of CTU and the Czech Institute of Informatics, Robotics, and Cybernetics (CIIRK). The launch allowed the institutes to join an elite group of European laser development centres operating similar workstations. Its uniqueness lies mainly in the number of laser applications located within a single cell, which can also be automatically and repeatedly changed during the process and thus processed by various technologies within a single production cycle.
Methodological settings under the supervision of LASCAM specialists
The entire cell is controlled by a parent Siemens SINUMERIK control system that controls the robot and additional axes. Peripherals such as the laser, extraction, wire feed, and triggering of the protective atmosphere gas are controlled by the PLC. Checking safety compliance is another important function of the PLC. The statuses of the emergency buttons and the closure of all cell entrances are checked to prevent laser radiation from escaping the work area. The working process itself is then controlled by an NC programme. The programme includes blocks determining the movement of the robot and blocks controlling the peripherals. Peripherals are controlled by M and H auxiliary functions. The Siemens NX environment has been used for off-line programming on a virtual workplace model (digital twin), including generating the NC code. The methodology of all these parameters and their time sequence in this project were handled by LASCAM specialists.
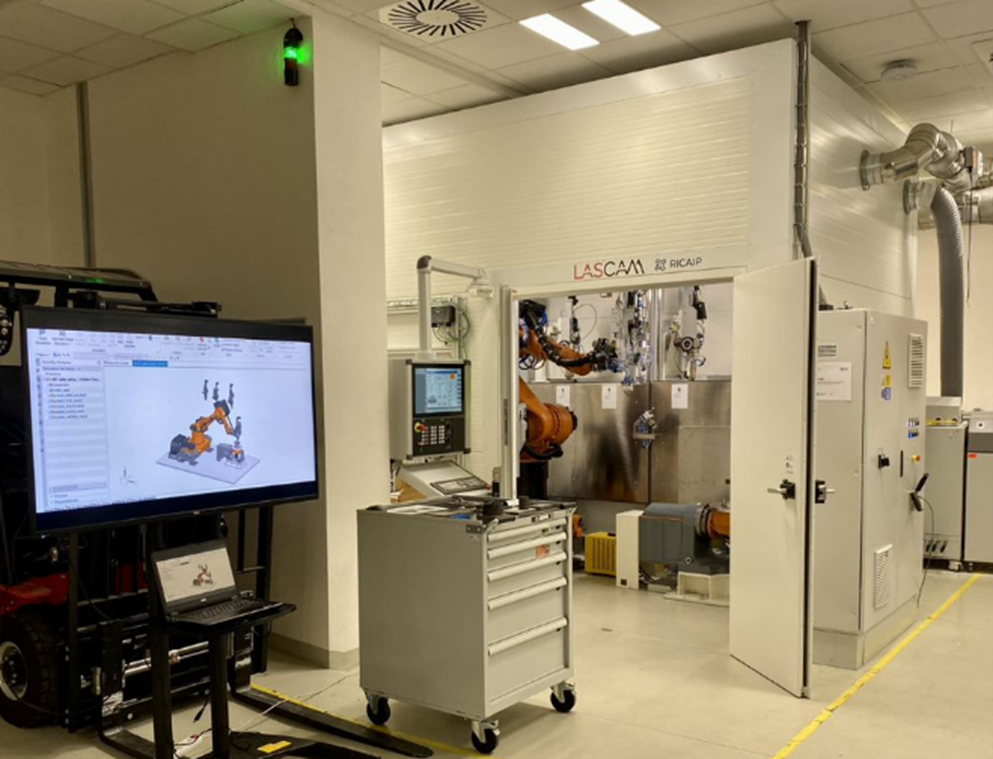
Internal equipment of the cell
The entire system is designed as a 9-axis system. Inside, the cell is equipped with a 6-axis robot, a linear slider, and a rotary folding table operating in two axes. Eight of the these nine axes can be synchronised, i.e. their reconfiguration can be done simultaneously and automatically.
Additionally, inside are installed four different laser process heads, which are linked to one laser radiation source with a maximum power of 6 kW and a wavelength of 1,070 nm. Process head replacement is fully automatic and can also be performed during processes.
3D laser cutting
Laser cutting is provided by the SolidCutter laser process head from Precitec, which can be operated up to 4 kW. The system is equipped with its own capacitive control, monitoring the distance from the material using its own Z axis. The workpiece is positioned using a rotary folding table with a load capacity of up to 500 kg. This makes it possible to move the part dynamically and synchronously during the process.
Powder welding
YC52 process optics from Precitec have been installed in the cell for powder welding. This is complemented by a fully automated powder feeder with heated jars, to avoid the process being affected by humidity. The installed technology allows the mixing of various powder materials to create different ratios of welded materials. In addition, if the powder is not mixed until during welding, the ratio in which the powders are mixed can be changed, and thus more durable properties of the resulting materials on the parts of the product that are more stressed can be exploited. The laser passes through the centre of the nozzle and a mixture of inert gas and powder is fed to the laser focal point. The inert gas serves not only to protect the welded material from oxidation, but also as a powder carrier. At the focal point, the powder is melted and welded onto the base material.
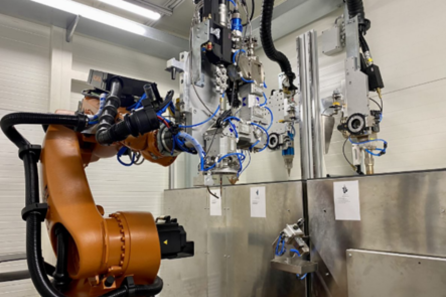
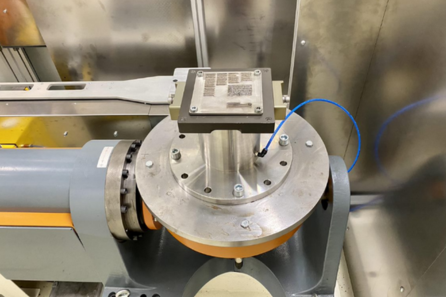
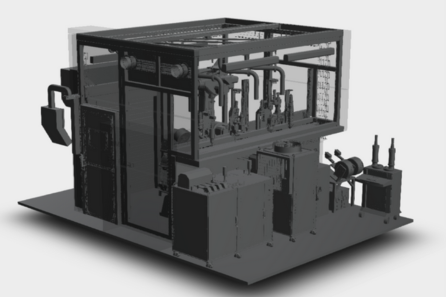
Laser welding using WOBBLE technology
The installed IPG Wobble Head D50 laser process head allows various oscillation shapes at frequencies up to 700 Hz (linear, ring, figure-of-eight or other user-generated shapes), which provides a significantly wider range of possibilities and results in high weld quality, especially when the welded materials do not completely fit (allowing optimisation of the bath for welding). The system is supplemented by an additional wire feeder with back control for the material feed stability.
3D printing with additional wire
The welding process is performed by the CoaxPrinter welding head from Precitec. This head allows the wire to be fed coaxially with the laser, which in turn allows welding in all directions. The laser exits the ring-shaped aperture and thus energy is supplied evenly into the process. To prevent oxidation, argon is fed into the process as a protective atmosphere.
Ready for the digital plant concept
The entire workstation is controlled by the parent system of the CIIRK building in Prague 6, Dejvice. Thanks to this, the cell can co-operate with other cells in the area and is thus fully integrated into the digital plant ecosystem that CIIRK has been developing. A typical example includes the use of automated product transport using AGV trolleys, thanks to which a semi-finished product can be exchanged without an operator entering the cell. The trolley uses its arm to pass the product into the cell on a sliding belt and the product travels inside, where the robot picks it up with its grab. After performing the laser process, the robot puts the product back on the belt, shifts it out of the cell and the AGV trolley picks it up again.
Use in industry
Thanks to this multifunctional cell, academic institutions have obtained a unique workspace for the testing (e.g. testing various types of powders) and development of laser processes and methodologies, which can then be implemented very quickly into existing conventional laser processes. It is especially applicable in the engineering, aerospace or automotive industries. It can be used, for example, for custom production, repairs of already worn parts, coatings to extend the service life of existing parts, or for the production of whole new parts.
Summary of the technical equipment
- Laser source – YLS 6000 with four process fibres
- Robotic arm – KUKA KRC 60 in HA (High Accuracy) modification
- Positioner – KUKA HV 500
- Control system – Siemens SINUMERIK 840D
- CAD/CAM software – Siemens NX
- 3D printing – Precitec CoaxPrinter
- Powder welding – Precitec YC52
- Welding using WOBBLE technology – IPG Wobble Head D50
- 3D cutting – Precitec SolidCutter