Industrial cleaning continues to evolve and innovate. One state-of-the-art method in this field is laser cleaning. It is harmless to the environment, has a wide application in numerous sectors, and achieves precise and effective results. This technology was also chosen by our customer, a leading manufacturer of car ceiling upholstery, as an alternative to cleaning using dry ice, sandblasting, pressurised water, and chemicals. For several years it has therefore been using our SPYRE 500 mobile laser unit to clean large-format forming tools.
Manual laser cleaning of large format forming tools using the SPYRE mobile unit
How does the laser cleaning process work?
During laser cleaning, all contaminations (such as material residues, separators, process greases, etc.) are removed from the surface of the material, which in most cases could only be removed by combining several various cleaning methods. One of the biggest advantages using a laser has brought is that the entire cleaning process takes place without breaking or thermally affecting the underlying layer of the material. The laser setting parameters can be very easily and intuitively adapted to the geometry of the part being cleaned. Thanks to this, dirt can be removed or layers cleaned both locally and over large areas, both indoors and outdoors.
Effective alternative to conventional cleaning methods
The aim of our project has been to replace cleaning with dry ice and chemicals, which is inefficient, costly, tremendously noisy, and non-eco-friendly. Using the latter, the customer used to laboriously remove separator residues, surface rust, and other operating contaminants from the large-format forming tools used to press the internal ceiling upholstery of cars and trucks. The technology was very expensive, time inefficient, and not environmentally friendly due to the generation of large amounts of waste and risk to the health of workers in the tool shop.
Therefore, at the customer’s request, an in-depth analysis of the process and testing was carried out directly in the production premises, and the SPYRE mobile cleaning unit (developed and manufactured by us, with suitable optics and 500 W of power) was recommended as the most suitable solution. The system was subsequently supplemented with a balancer and fitted with a tailor-made attachment and travel wheels to enable the laser head to be handled more easily over the surface of the forming tool/mould.
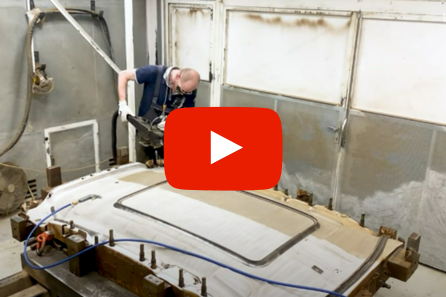
SPYRE mobile laser cleaning units are the perfect solution in lots of different cases of industrial laser cleaning. The system relies on laser ablation technology using very short pulses with high peak power. The laser beam acts directly on the dirt and removes it through the thermal expansion of the dirt on the substrate owing to the introduction of high energy, thus effectively ‘blasting’ the dirt away from the substrate and so minimising the risk of surface damage. The system allows for precise adjustment of the laser beam’s parameters, such as energy intensity, frequency, and spot size. This enables you to optimally clean various types of dirt and surfaces, thereby minimising the need for additional manual cleaning. SPYRE has been designed as a virtually maintenance-free device that can be used easily and immediately.
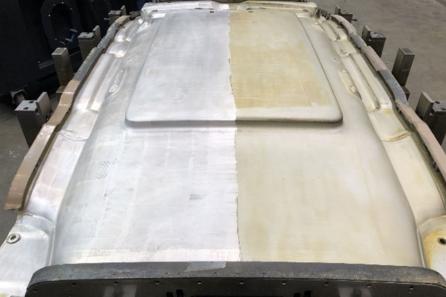
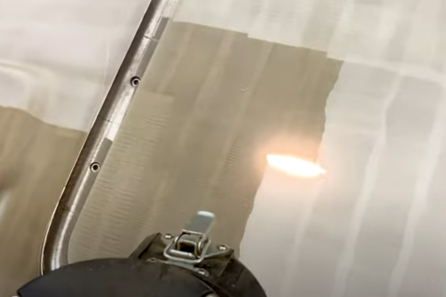
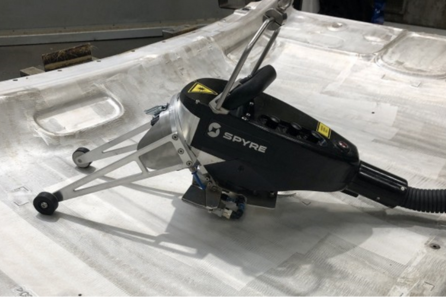
Main benefits of the project
The successful integration of a SPYRE mobile laser cleaning system into operation has generated significant cost savings compared to the original cleaning technology. It has completely eliminated any need to purchase very expensive consumables (dry ice, chemicals, compressed air) as well as their storage and the subsequent waste disposal after cleaning. The customer cleans twice as many forming tools per shift with only one operator instead of the previous two. The racket of the dry ice cleaning process has also been massively reduced. Last but not least, thanks to the use of laser cleaning technology, no material is removed, and thus there is no associated damage to the forming tool, which guarantees the extension of its overall service life and service cycles.
Features and benefits of the solution:
- Reduction of cleaning time by half compared to the original technology
- Reduction of the number of operators per shift – currently one instead of two
- Zero cost of purchasing and storing consumables
- No disposal of hazardous waste from dry cleaning
- Noise reduction at the workplace
- Eliminating damage to the forming tool during cleaning and therefore extending its service life and service cycles
- Possibility to clean both cold and hot moulds directly in the press or tool shop
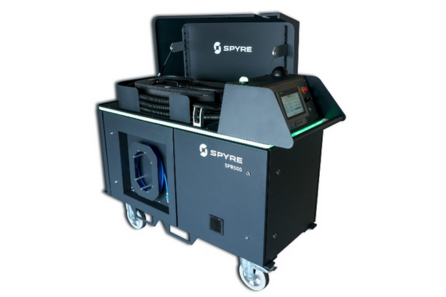